ASE SNAT Co. applies its Quality Assurance System and Quality Control plan in order to ensure that the responsibility of quality determining activities are documented and clearly identified.
The Quality System covers the planning, performance, verification and review of all activities, which affect the ASE SANAT’s ability to comply with specified requirements.
The Project Quality Plan has been prepared on the basis of the following documents:
- Contract
- ISO 3834 (Quality Requirements for Fusion Welding of Metallic Materials)
- ISO 9001 (Quality Management Systems-Requirements)
- OHSAS 18001 (Occupational Health and Safety Assessment Series)
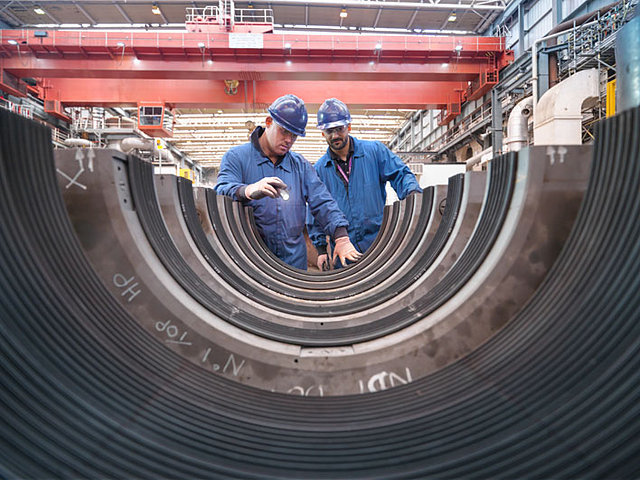
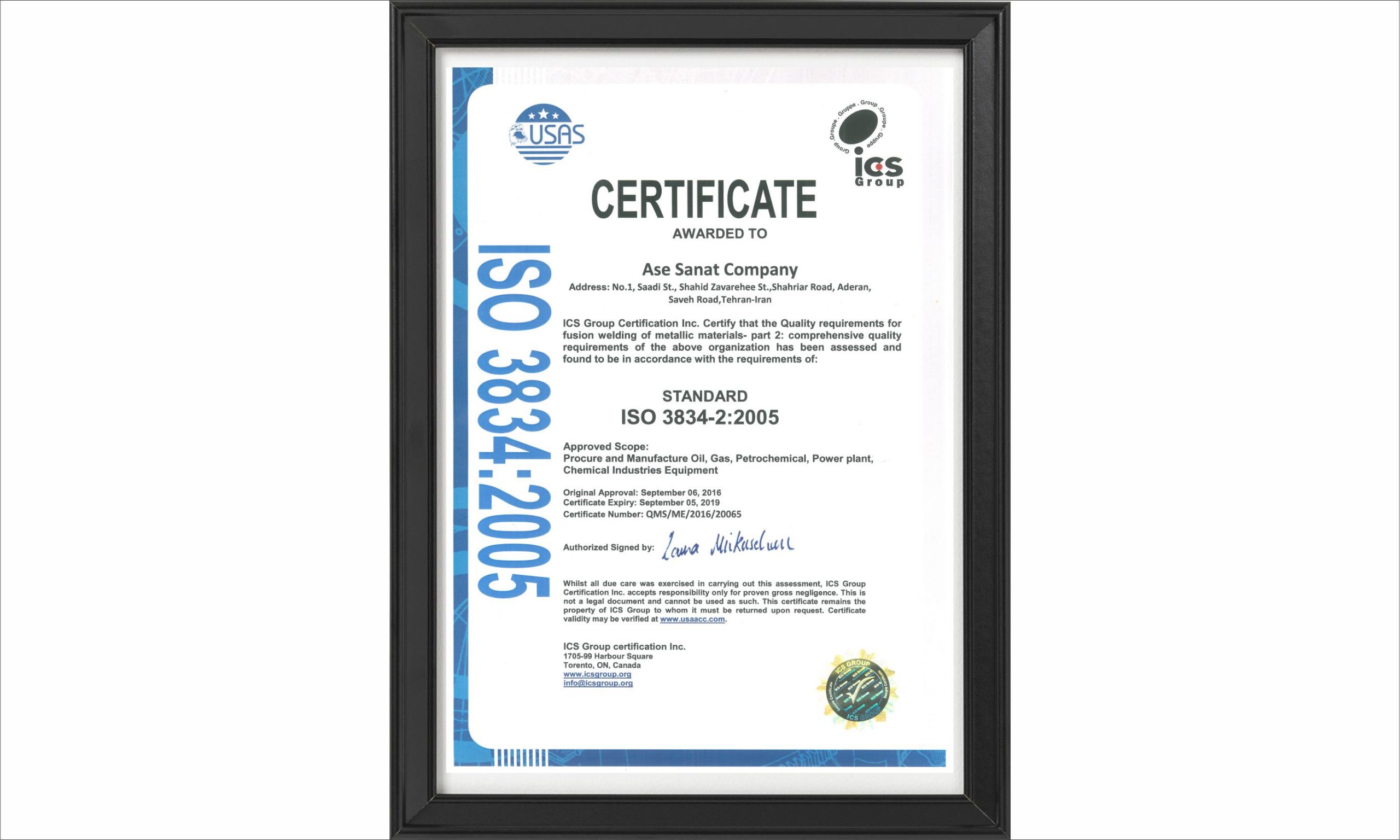
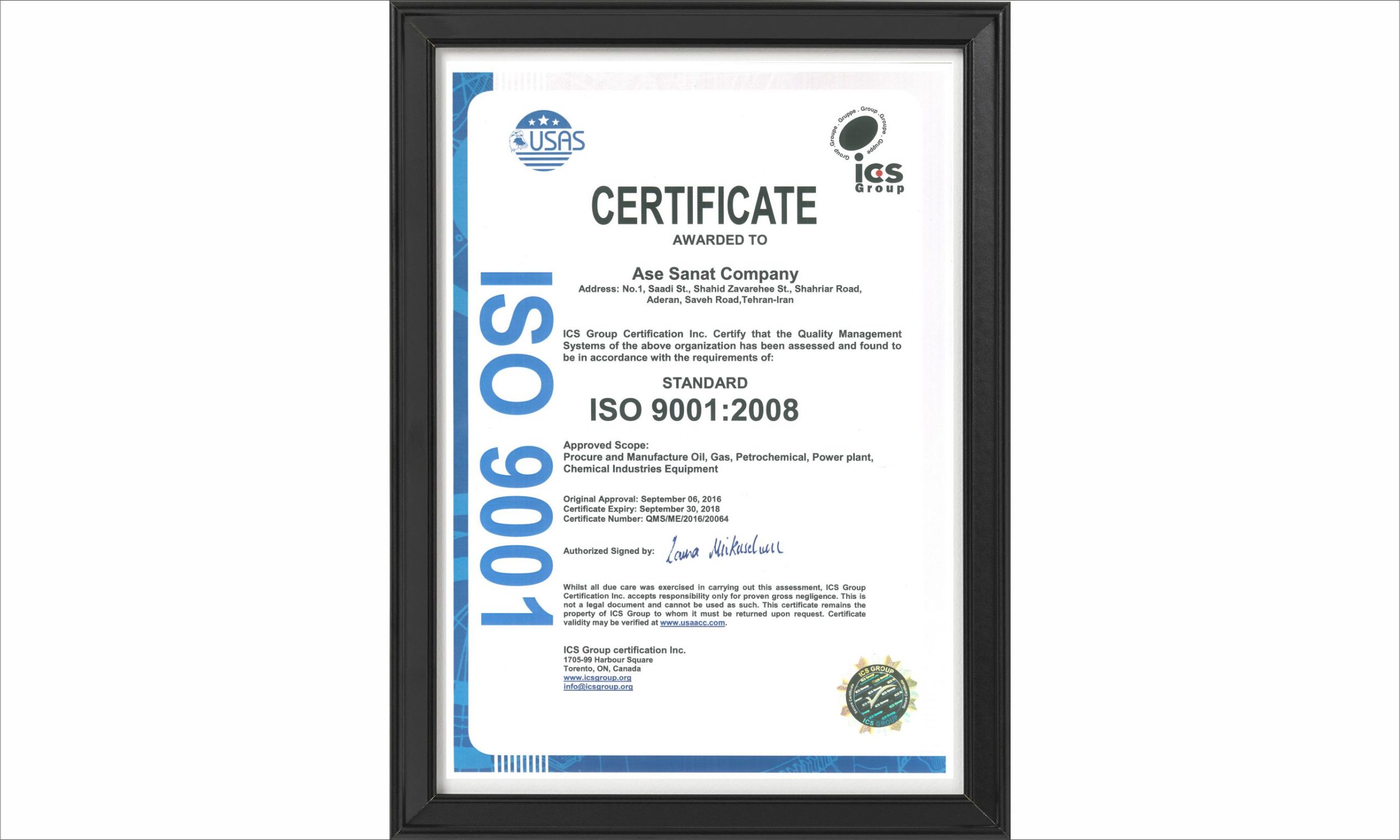
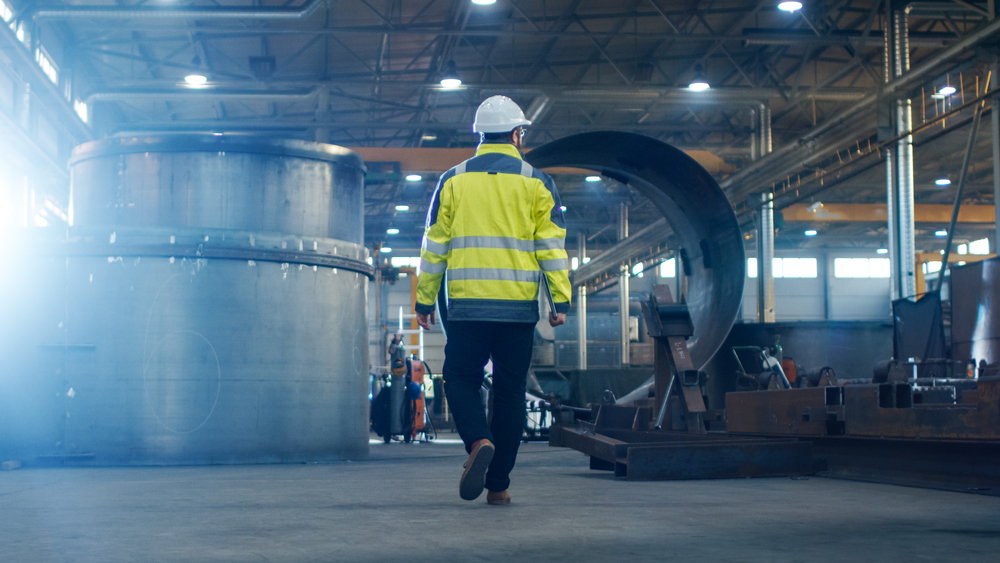
QA/QC Manager completely surveys project quality plan implementation, development and maintenance to make sure that project execution meets contractual requirements:
- Receiving Material Inspection and Testing
All received material/equipment shall be inspected by QA/QC inspectors before entrance to site in order to make sure that purchased goods will meet the project specifications which have been stated in purchase request forms and if they have any defects, damage, shortage or losses. In case needed, necessary physical examinations are also performed. Such inspections are done according to inspection test plan and result will have recorded.
- In-Process Inspection and Testing
For all project activities, required inspection and testing are implemented according to inspection and test plan and test procedure. Result of such inspection and testing are recorded to make sure that different stages are verified according to methods formerly determined.
- Final Inspection and Testing
For all project activities final inspection and test will be performed during pre-commissioning stage in order to ensure all requirements of inspection and testing are implemented according to inspection and test plan and test procedure and commissioning procedure. Result of such inspection and testing are recorded to make sure that different stages are verified according to methods formerly determined.
All non-conformity status shall be clarified during project. Reporting of non-conformances which are not identified during internal audit, shall be the responsibility of the relevant discipline managers, engineer(s) and it shall be reported to QA/QC for controlling and tracing in order to ensure the problem will be removed. It shall be the responsibility of the relevant Discipline Manager Engineer(s) to issue corrective actions for reported non-conformities. Each discipline is informed during the internal quality audit and non-conformities shall be registered and reported in the audit reports.
The vendor shall be responsible for taking any necessary corrective actions, as a result of a reported non-conformance’s during inspection and test activities at Vendor’s shop.
Preventive actions shall be implemented according to appropriate method statement and it shall be available and traceable by QA/QC for next follow up.